Welcome to the future of metals manufacturing, where sensor technologies and 5G connectivity usher in a new era of industrial innovation. Such optimization enhances operations, minimizes waste, and elevates product quality.
This article explores how these cutting-edge developments are transforming traditional factories and base metals market, boosting both productivity and sustainability. Discover the power of smart, interconnected systems as they propel the metals industry into a realm of unparalleled efficiency.
Driving advancements in metals manufacturing
In the last ten years, automation has really changed the game in manufacturing. It’s not that automation itself is new, but the way we’re using it has shifted, giving manufacturers more control over how things get done. This shift makes it easier to automate boring, dangerous, or repetitive tasks. From loading and unloading to processing and assembly, many processes now need minimal human involvement.
The metals industry, a key player in supply chains like construction, automotive, aerospace, and electronics, has reaped the benefits of these changes. Even with challenges like fluctuating commodity prices, regulatory pressures, and environmental issues, the industry is looking toward digitalization and automation to boost resilience, cut costs, and lessen environmental impact.
These strategies will be vital as the industry adjusts to global economic changes and the increasing demand for metals driven by tech advancements and industrial growth.
Sensors in manufacturing environments
Sensors are crucial for keeping tabs on manufacturing processes across different industries. Smart sensors can gather data and send it to central cloud systems for analysis, making Industry 4.0 practices more accessible. Both humans and machines can access and track this data, leading to better decision-making.
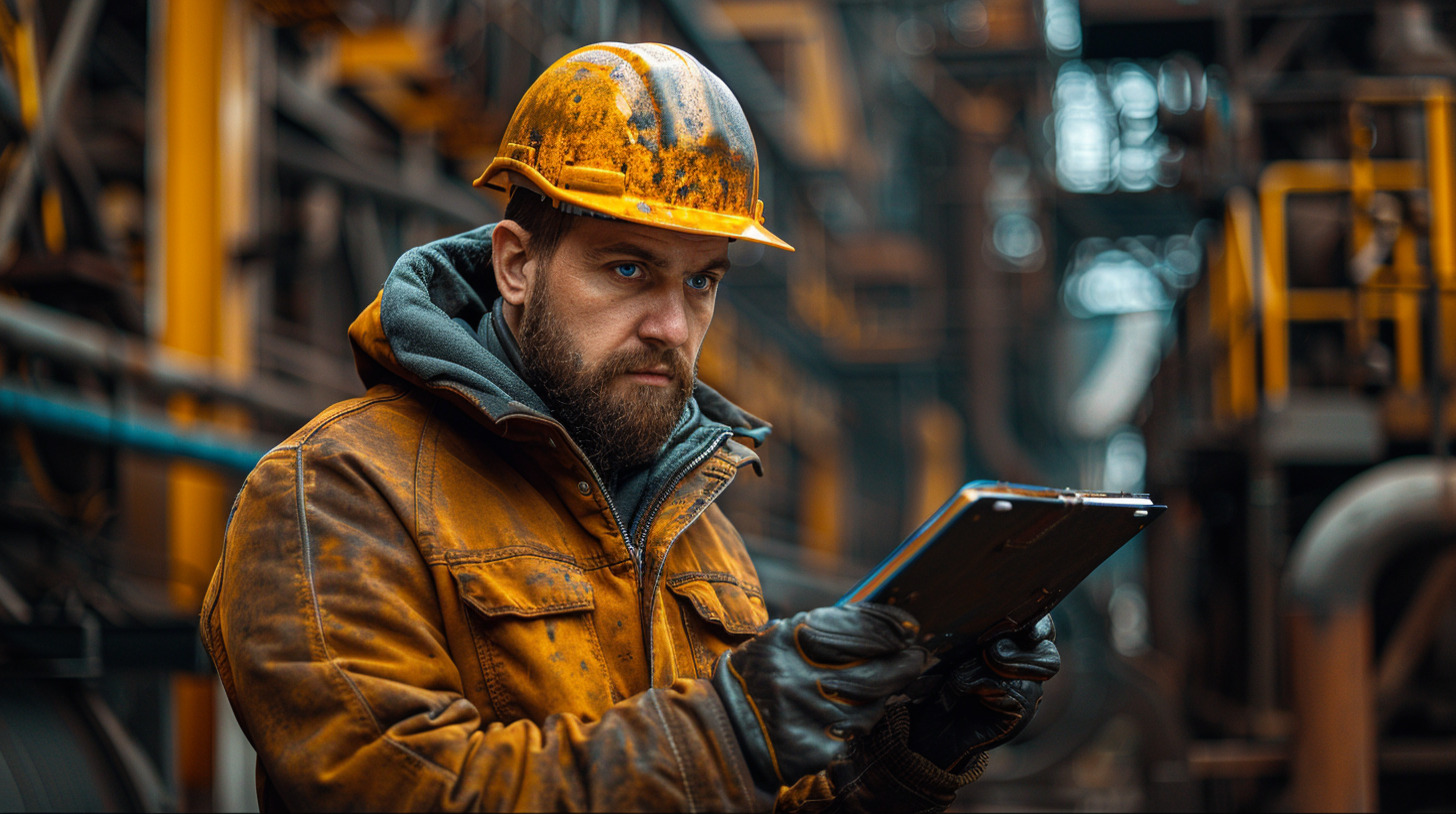
Sensors for machine monitoring
In specialized applications, sensors watch over and get to know the “normal state” or “signature” of a whole machine’s output. Algorithms then keep an eye on this signature much faster than humans can, providing feedback to operators and maintenance teams, allowing for predictive maintenance before things go south.
A use case in metal manufacturing
At one of Europe’s biggest steelmaking sites, specialized sensors and monitoring software are giving some much-needed operational insights. Using electrical signature analysis (ESA), the system checks out the health and performance of 100 conveyor rolls in tough conditions, spotting issues like mechanical imbalance early on.
This proactive approach cuts down on downtime, with initial successes leading to a wider rollout for better maintenance efficiency.
The transition to interconnected systems
Sensors can move from being standalone tools to being part of an integrated network, boosting manufacturing insights and process accuracy. This networked system helps with robust data cross-checks and full environmental monitoring.
To scale these sensor systems effectively, you need advanced connectivity to avoid high costs and inefficiencies, highlighting the need to consider the full network infrastructure when planning deployments.
Connecting the dots: 5G on the factory floor
Sensors have gone from being isolated gadgets to being part of interconnected networks, significantly boosting the precision and efficiency of metal manufacturing. Here are some key benefits and things to think about before diving into integration:
- Enhanced insights: Networked sensors offer a complete view by cross-validating data and monitoring environmental conditions.
- Process accuracy: Mixing different sensor types can improve the accuracy and reliability of manufacturing feedback systems.
- Scalability challenges: Scaling up effectively needs strong network systems to keep costs down and efficiency up.
- Infrastructure considerations: The whole manufacturing network infrastructure should be taken into account when rolling out advanced sensor systems.